Online Parts Catalog
Wednesday, January 26, 2022
3 Tips for Surviving the Ongoing Aftermarket Parts Shortage
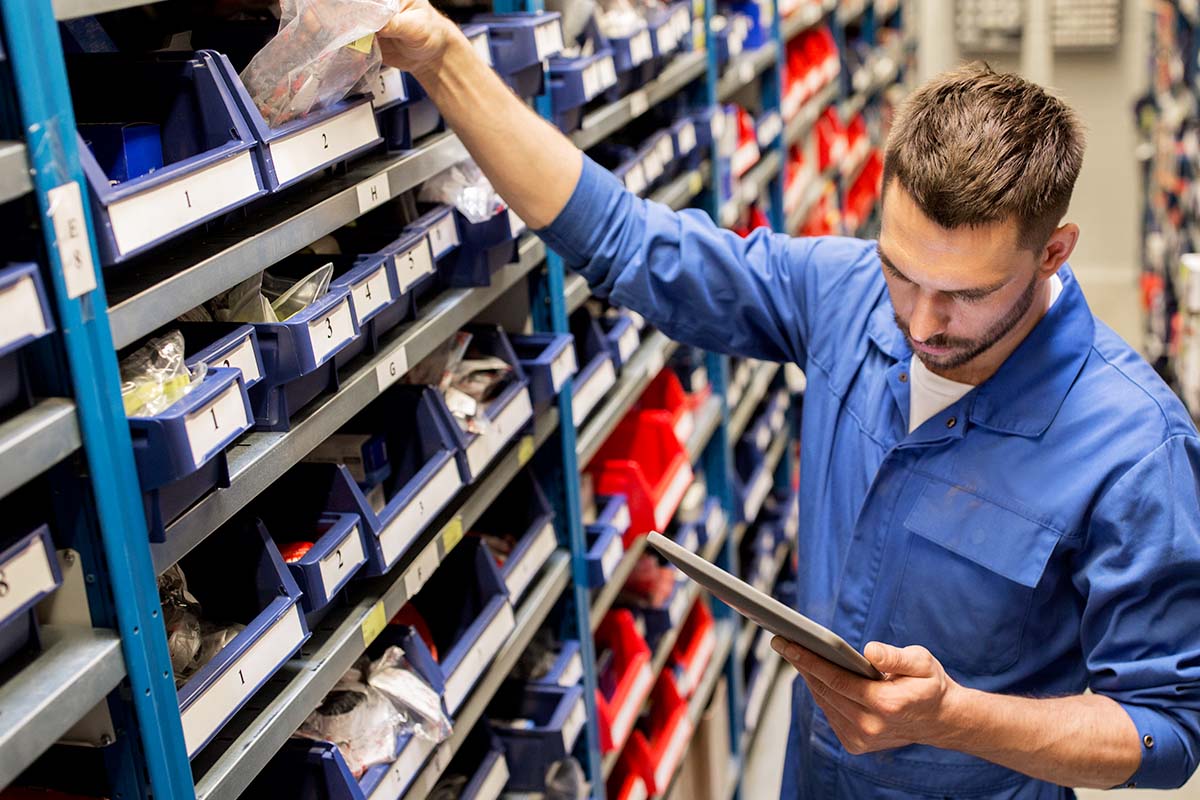
It’s not just the OE manufacturers that are having difficulty finding parts. Many fleets are continuing to experience extended wait times for aftermarket parts due to the Great Supply Chain Disruption.
To help fleets weather the ongoing shortage in the best way possible, here are some best practices to consider for optimizing heavy-duty part inventories:
1. Mine Your VRMS Data
Vehicle Maintenance Reporting Standards help standardize part numbers no matter what dealer or distributor is used to acquire heavy-duty parts. This can make it easier to determine what parts a fleet has on hand, where they are and what may still need to be ordered.
Maintenance records and vehicle makes/model information are critical data points fleets should be able to pull up at a moment’s notice. Segmenting parts by routine maintenance and sudden repair events can also provide more actionable data that can be used to address unexpected equipment breakdowns. To make the most of this data, fleets should have a dedicated distributor who can help them get these emergency parts in the shop within 24 hours or less.
Part lead times should also be considered and recorded in the event fleets may need to modify order frequency and quantities. The goal should be to ensure there is always a reasonable number of parts on the shelf during a shortage.
2. Count Parts that Fly Off the Shelves
Making sure to schedule a weekly or monthly physical inventory check for the parts that get used the most can help ensure a healthy level of the most in-demand parts like filters, tires and brake pads.
Break out the calculator or excel spreadsheet to assess how many days stock you have left for each part and set minimum quantity levels that ensure you don’t stock too little or too much. On average, it costs 15-30% of a business’s total inventory value just to keep products in stock, depending on how efficient an operation’s inventory management processes and controls are.
It should go without saying, but as soon as parts are pulled from the shelves to make a repair, they should be recorded. Additionally, parts that were needed but not in stock at the time should be documented and outstanding purchase orders should be watched and closed shortly after parts are delivered.
3. Reach Out to Suppliers & Distributors
Fleets should consider working with distributors and dealers who can identify the location of the part you are looking for in real-time.
While the parts may not be sitting on a shelf at the local distributor, they may be able to use technology to pinpoint where another distributor has that particular part in their network. Additionally, they may also have insights from the supplier that can be used for making more accurate decisions on future inventory purchasing.
Taking Control
With the high demand for freight and less volume of new heavy-duty trucks available, fleets need to do everything they can to maximize vehicle uptime. That requires taking a more hands-on approach to parts data and communicating with vendors early in the process to find mission-critical parts sooner rather than later.
By using more accurate inventory reporting and forecasting, fleets can also keep average carrying costs lower, which helps maximize profits.
To find the right filter for a specific heavy-duty application, visit Luber-finer’s online parts catalog or download the Luber-finer app.